Komo Router Overview
Types of Screws
There are several types of ball screws assemblies found in the KOMO CNC Routers; commonly Japanese THK/NSK or Bosch Rexroth in later machines.
The Japanese external rotation bearing screw typically has two parallel tracks which run up and down the screw shaft on both the X and Y Axis. These ball screws are well constructed, with precision machined metal internal bearing circulation parts. They are the longest lasting and most durable of the ball screw types found in KOMO routers. While they still get clogged and starved for lubrication, they seldom fail to the point they cannot be refurbished and rebuilt. It is recommended the X-Axis be rebuilt every 3-5 years while in wood shop application due to fine sawdust debris collecting inside the ball nut assembly.
The Bosch Rexroth type screw is typically identified by four tightly wound tracks on the ball screw shaft with only one track in use. While the unused bearing races are convenient for rebuilding the ball screw, the load of the ball nut is nearly twice that of the Japanese THK/NSK screw type. It is recommended the X-Axis be rebuilt every 2-3 years while in wood shop application.
Bosch Rexoth
There are two main flaws with the Bosch Rexoth ball screw design. The "plugs" and the lubrication system.
The first flaw is the material used in what we call the "Ball Bearing Recirculation Inserts". These plastic parts are responsible for scooping ball bearings off the ball screw raceway winding, picking them up off the track and recirculating the ball bearings to the other end of the ball nut, and dropping them back on the track. Because these critical parts are made from plastic, they can wear quickly and crack, blocking the return of the ball bearings, possibly seizing the axis. However, if the ball screw assembly is kept totally clean, with a steady stream of lubricant, the Rexroth screws can last a long time.
The second flaw in the Rexroth design is the lubrication system. The main lubrication to the internal ball nut on the ball screw is provided by an oil line fitted to an external rotation bearing (made by INA of Germany) with two passive inner holes that reach the inner ball nut. As the nut is packed with contaminants, the two single drip lube ports inside the nut get clogged. With very little pressure to force the grit out of the ports, the screw and bearing are gradually starved of oil.
Once the ball nut assembly is packed with sawdust and the lube stops, the ball bearings stop rolling, eventually degrading the raceways and the other bearings. This typically is where the loud cement mixer grumbling sound starts.
Because the ball screw is loaded with machine tool grade chrome steel bearings, this skidding eventually causes the hardface surface of the bearings to start peeling off. Ball bearings are much like Tootsie Roll Pops. They have a very hard outside coating on top of a softer steel core. Ball screws pushed without lubrication and damaged balls eventually seize causing balls to distort or shear, locking up the screw and / or damaging the raceways of both ball nut and shaft.
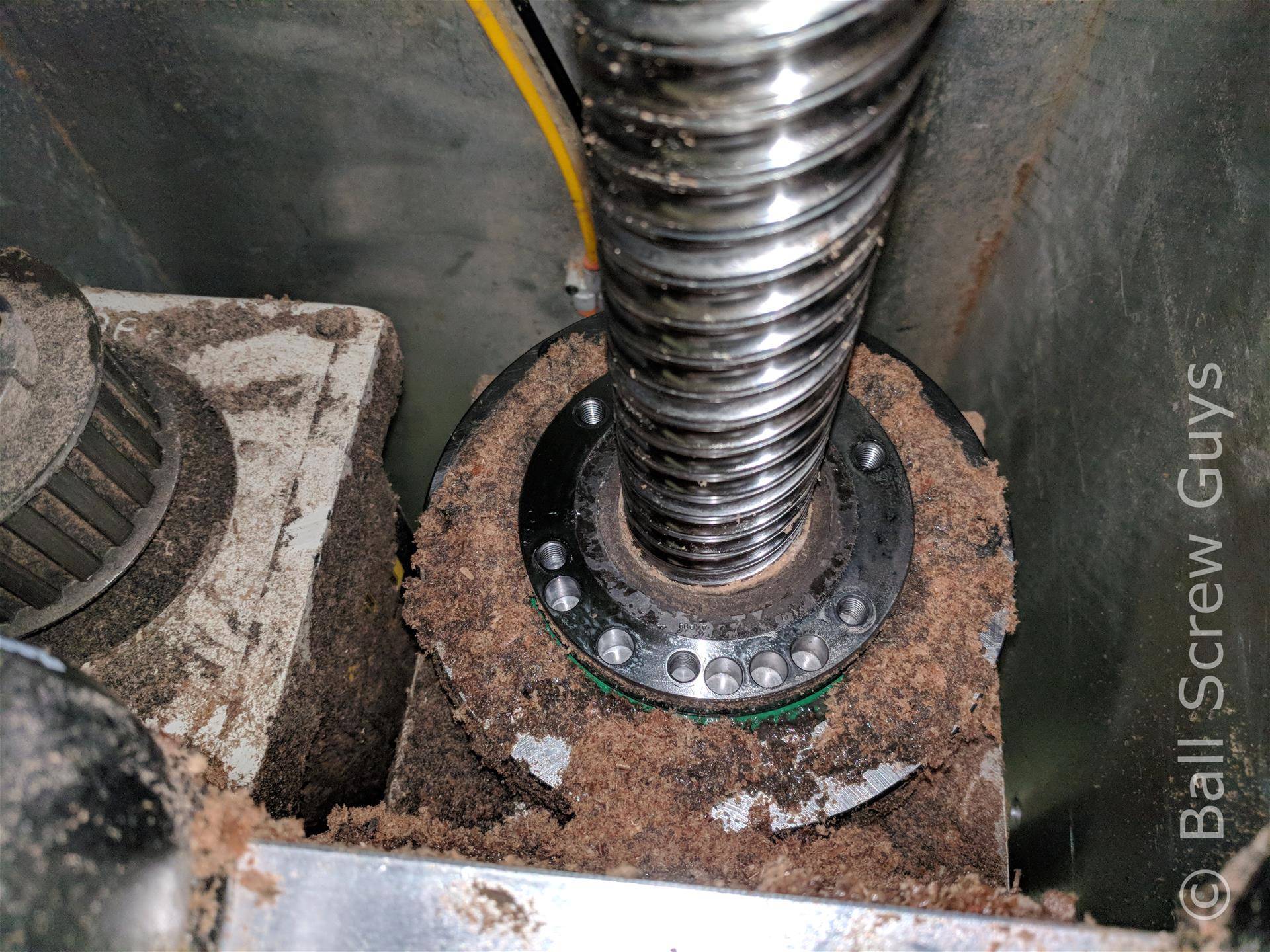
A Bosch Rexroth type screw with drive belt and pulley removed. The outer rotation bearing (green) is covered in sawdust clinging to the lubricant. Plenty of lubrication here. Notice the inner seal around the screw covered in a finer, dry grit. This is where the Pulley connects. Sawdust is left on the screw, usually from operators cleaning under the machine with an air hose. This material collects and gets crammed into the ball nut like an auger.
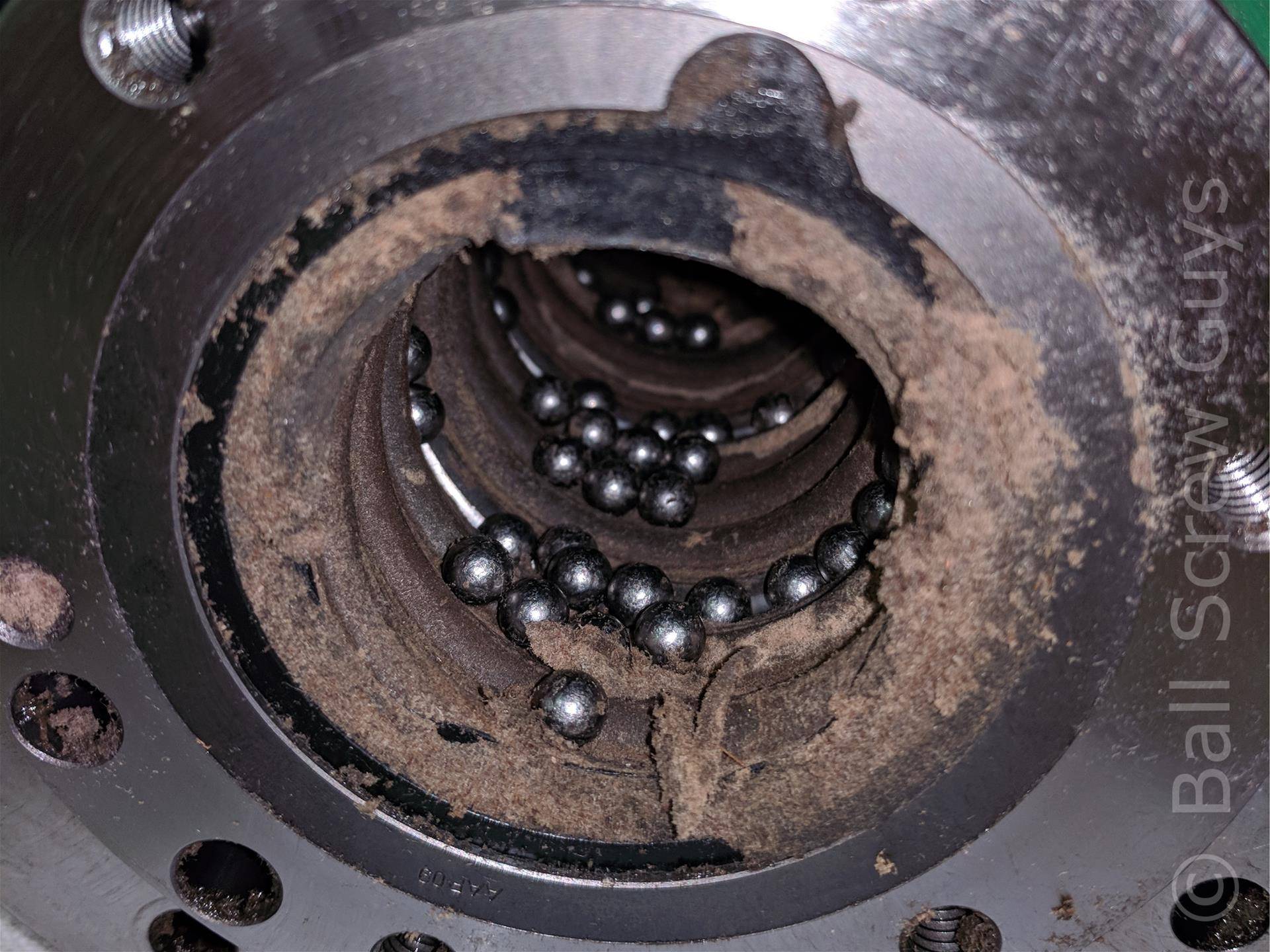
Loose bearings within the ball nut assembly. Zoom to view the pitting of the chrome steel ball bearings within. Notice the single raceway used for ball bearings. Over time, sawdust gets packed into the ball nut of your KOMO. This causes the bearings to bind in the raceways and clogs the oil lubrication system. This image is why your KOMO needs regular service.
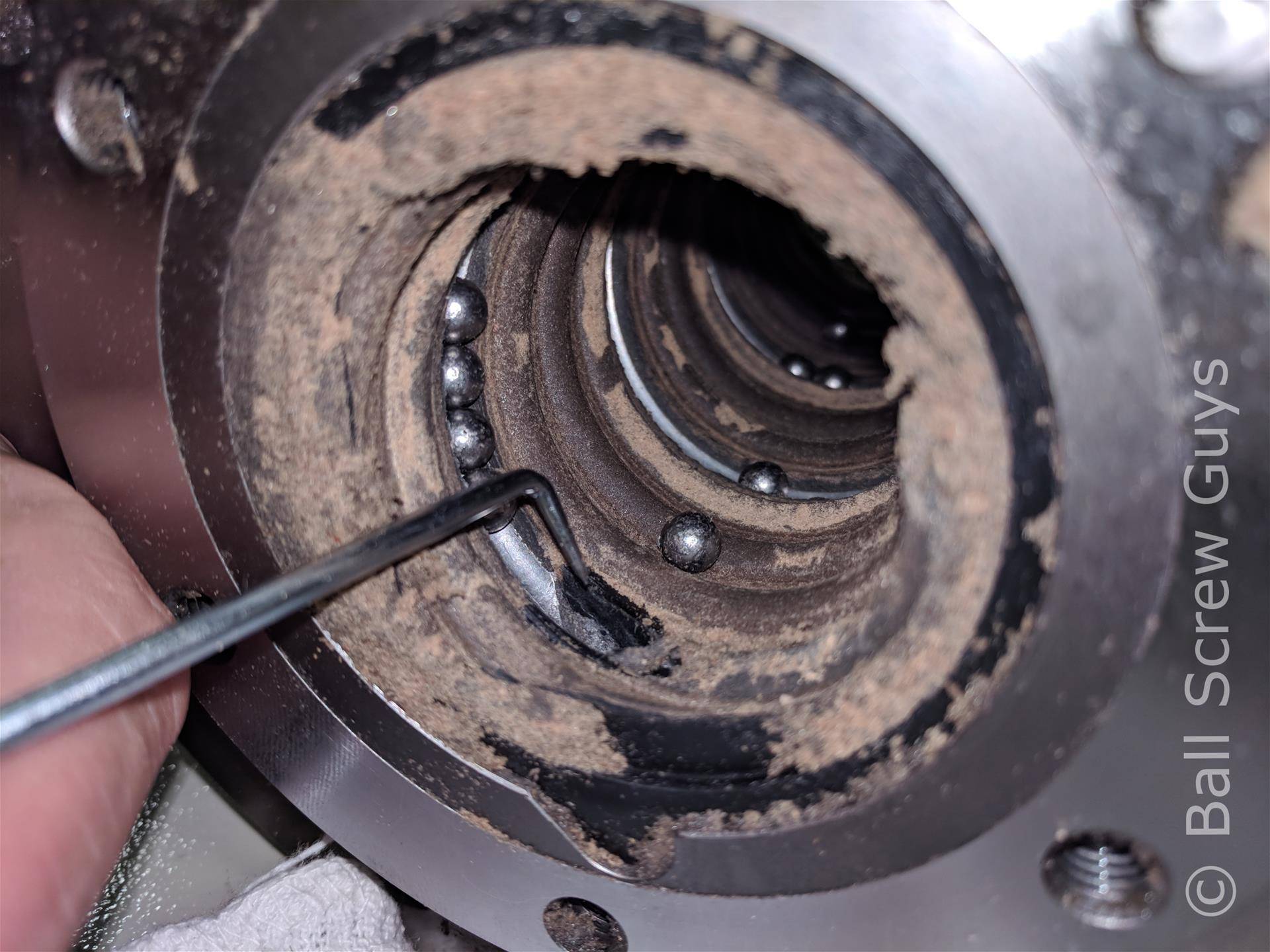
The Bosch Rexroth ball screws have plastic "scoops" which pick up ball bearings off the shaft raceways. These original OEM parts are plastic and commonly fail when the ball nut gets packed with debris. Ballscrew Guys has Brass Replacement Recirculation Plugs IN STOCK for all the Bosch Rexroth ball screws. There are many different sizes and variations of these bearing return inserts. Ballscrew Guys makes all the major types found in all the Rexroth ballscrew assemblies found in KOMO machines. From the smaller Y-Axis versions found in single table machines, the yet bigger size found in the X-Axis (Y & V on Dual Table Systems), as well as the monster X-Axis ball screw found on the dual table machines.
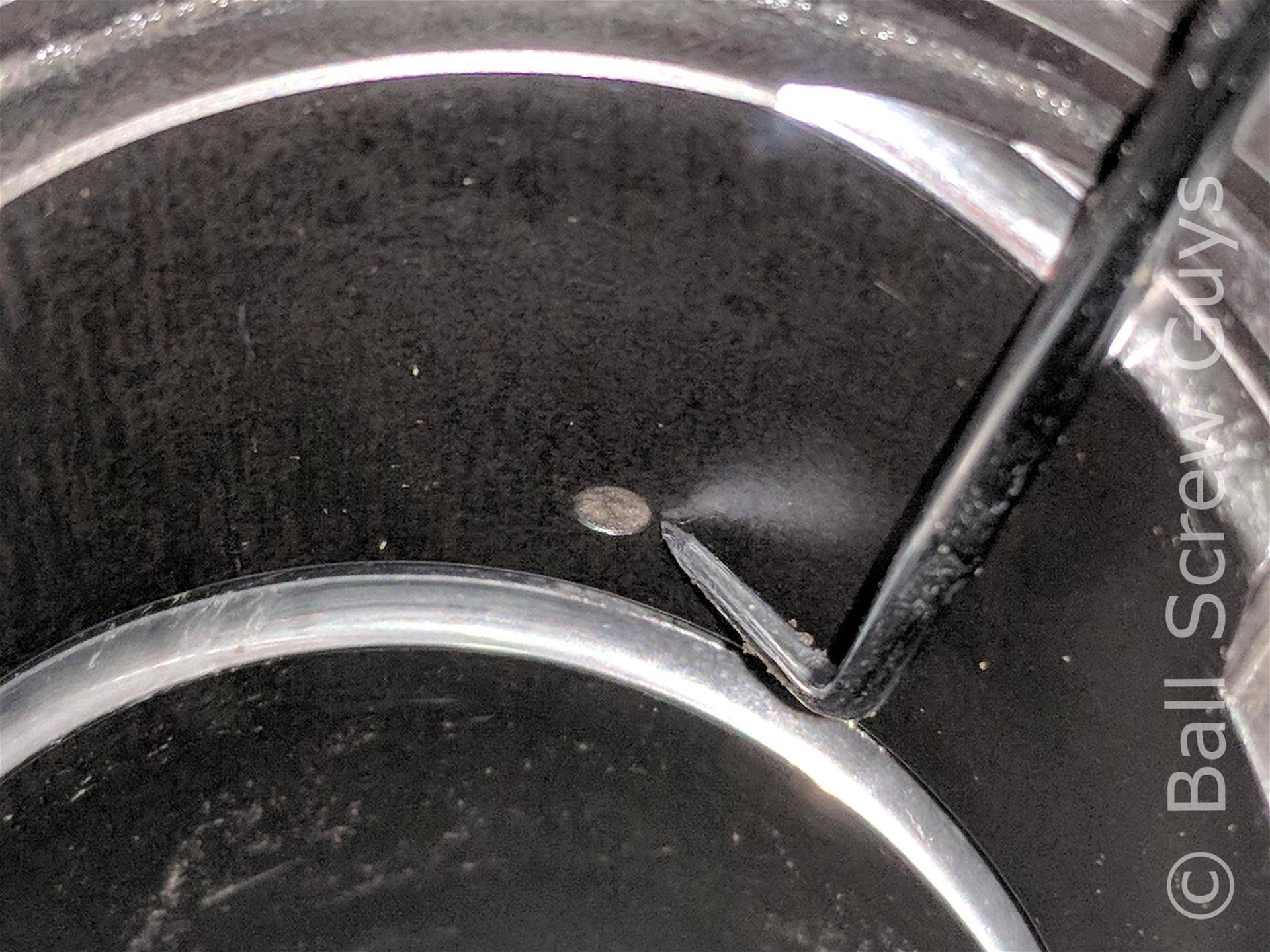
Blocked lubrication ports in a Rexroth ballnut. The passive oil based lube system can quickly clog up with fine grit, causing the bearing race to go dry. These ports must be cleaned out regularly.
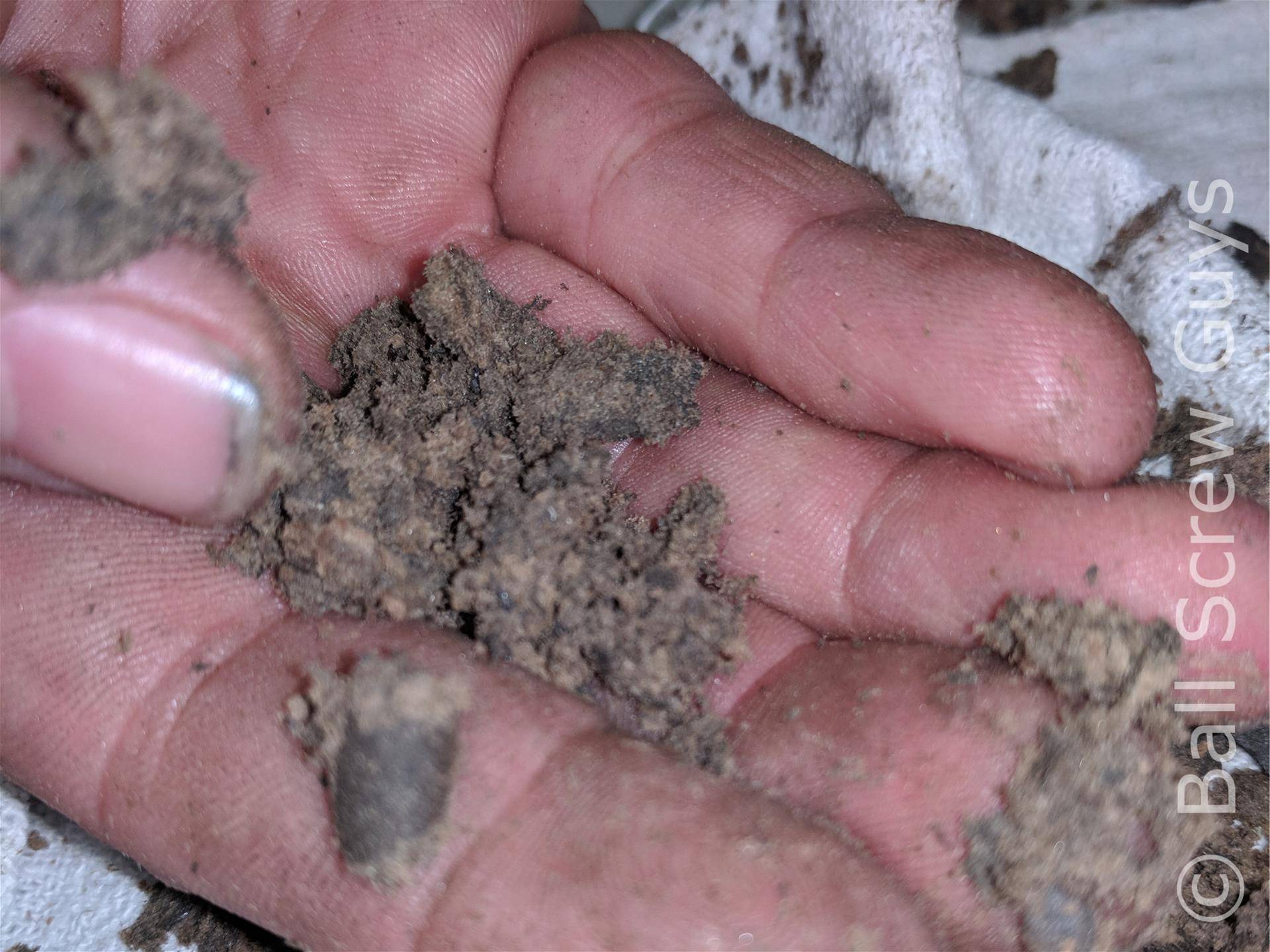
Fine sawdust is gradually forced into the ball nut assembly. While proper lubrication allows the bearings to roll freely, blowing sawdust onto the slightly lubricated ball screw builds up inside the ballnut.
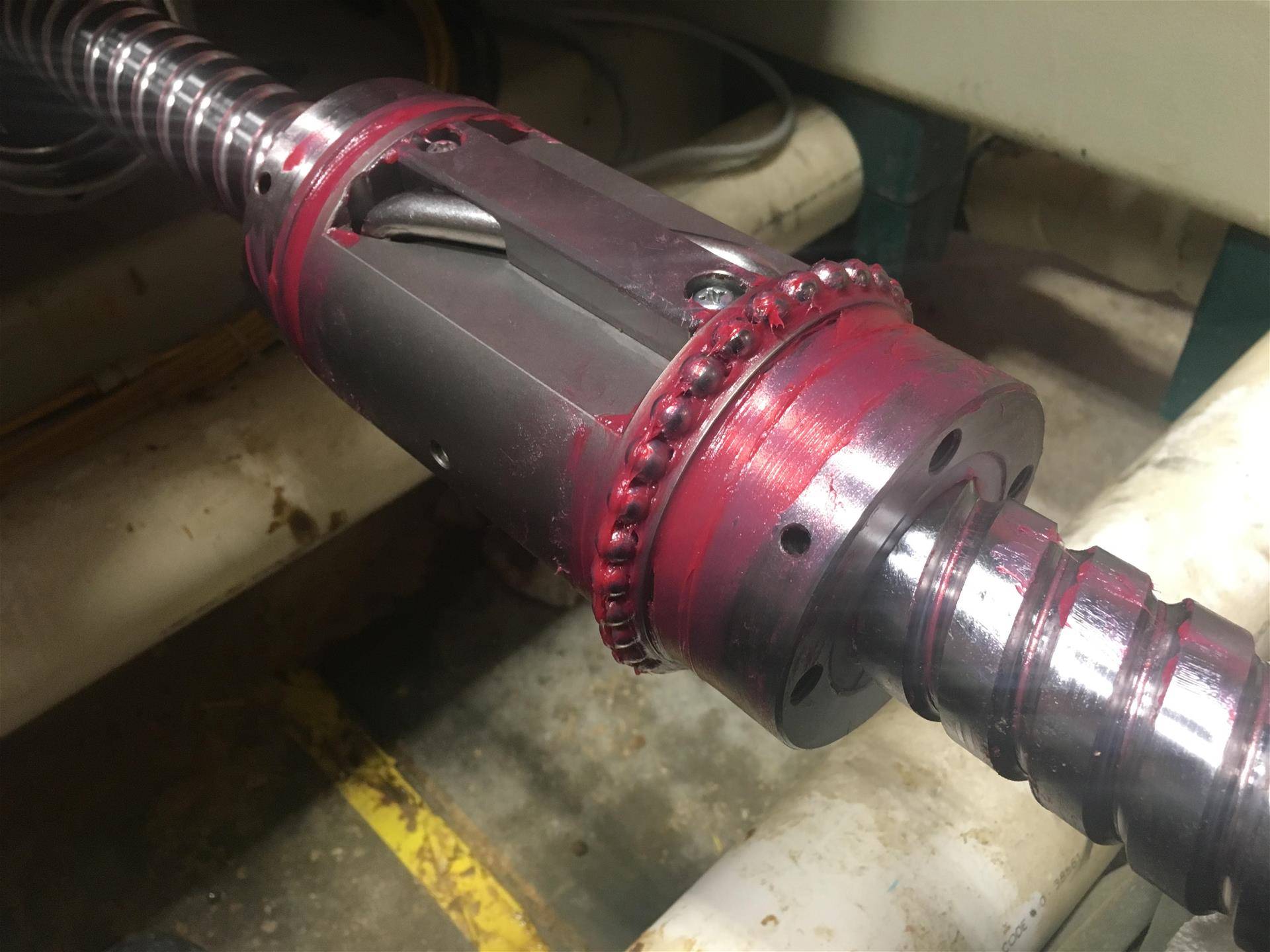
Japanese NSK type ball screws are found mainly older Komo machines. These are generally made all of steel and are extremely durable. You can tell this type from the Bosch Rexroth by looking at the ball screw lead itself. These types of screws will have two parallel bearing raceways. The interior ball nut rides on both of these tracks. Above is the inside ball nut with the external rotation bearing removed. This image shows us rebuilding the external rotation bearing. Ballscrew guys combines the price of External Rotation Bearings with the basic price rebuilding the ballscrew.
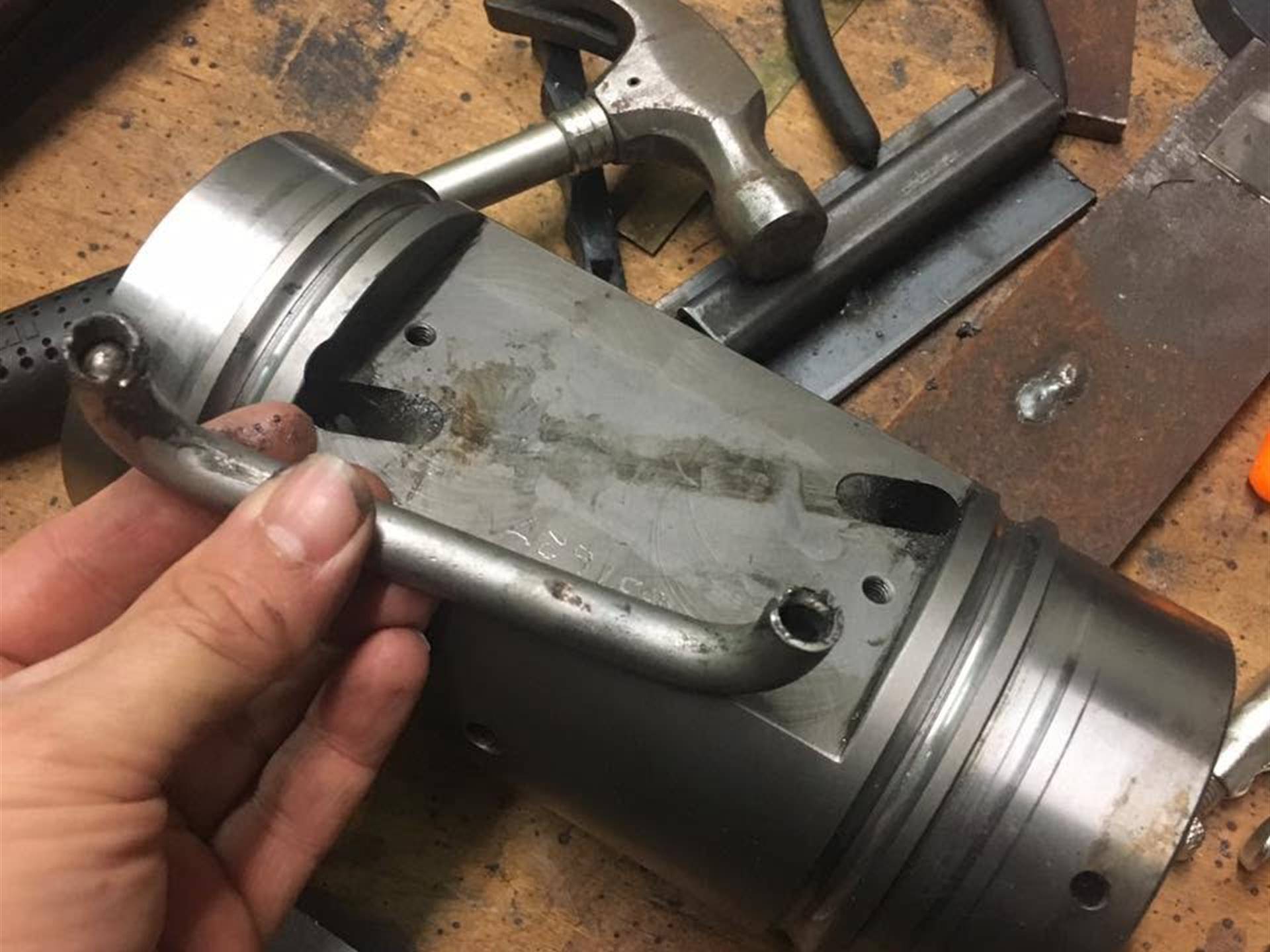
While these Japanese screws are well constructed with metal ball bearing circulation return tubes, they will still fail if left unattended. Ball screws on routers must be periodically cleaned and flushed out, otherwise the ball bearings stop rolling. Eventually causing the screw assembly to seize, sheering off the "scoop tabs" of the steel return tubes. We can fix this issue in most cases, but cannot emphasize enough how important it is to rebuild your screw before this critical failure. Regardless, Ballscrew Guys have Certified Welders (TIG/GTAW AWS D1.1 and ASME Sec.IX All Position Unlimited Thickness) with the skills to refurbish your existing tubes even if damaged. Should this not be an option, we also have the means to fabricate new tubes, however there may be a lead time to make this happen.
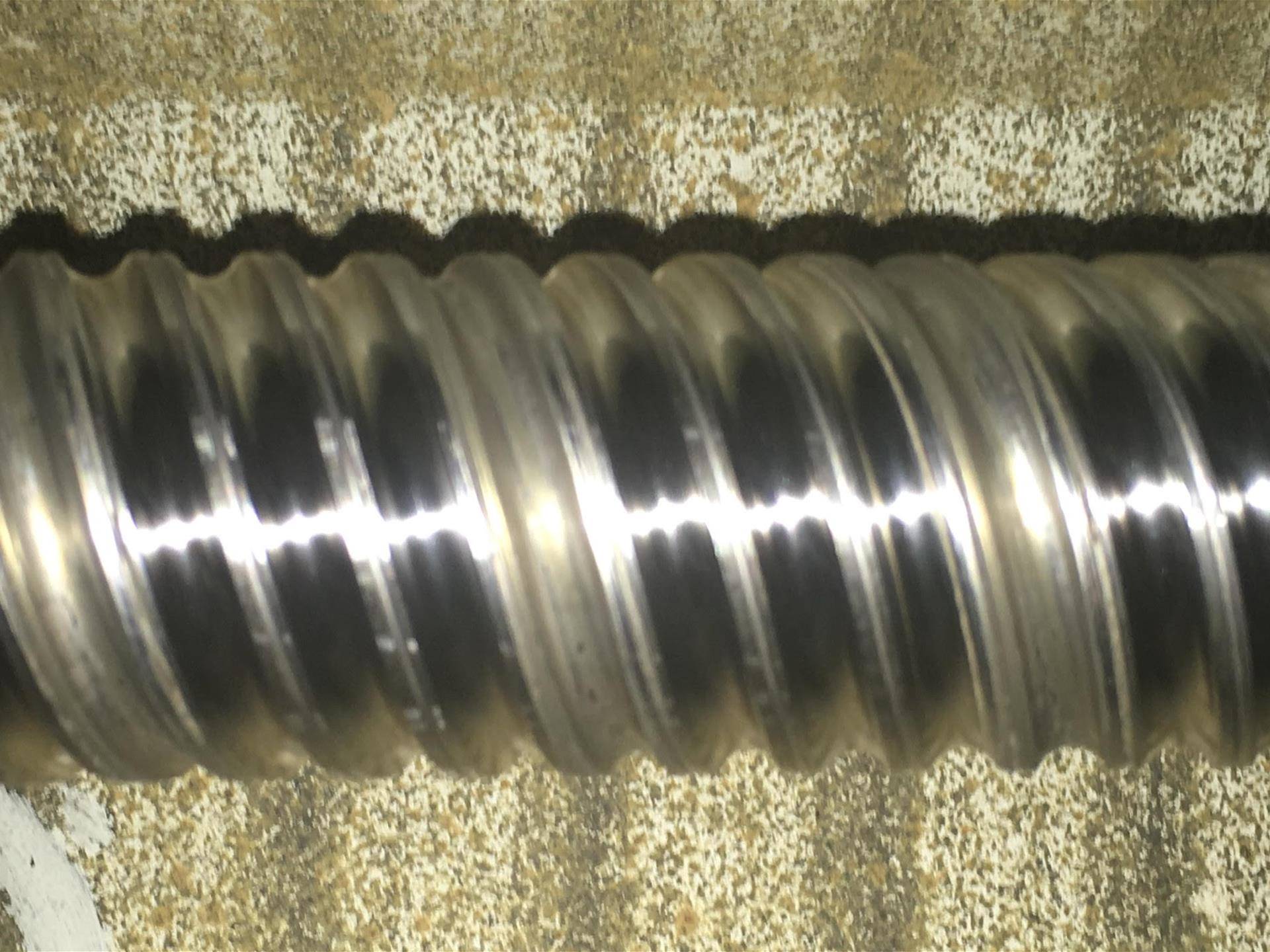
One of the best ways to see if your Rexroth type screw needs service is to inspect the ball screw itself. If the ball screw is starved for lubrication or heavily contaminated, it will often leave a "streak" or marking in the raceway track the ball bearings run in. While the ball screw shaft itself has 4 separate grooves, the ball nut only rides on one of them. As long as the screw remains undamaged, the entire assembly can be rebuilt many times.
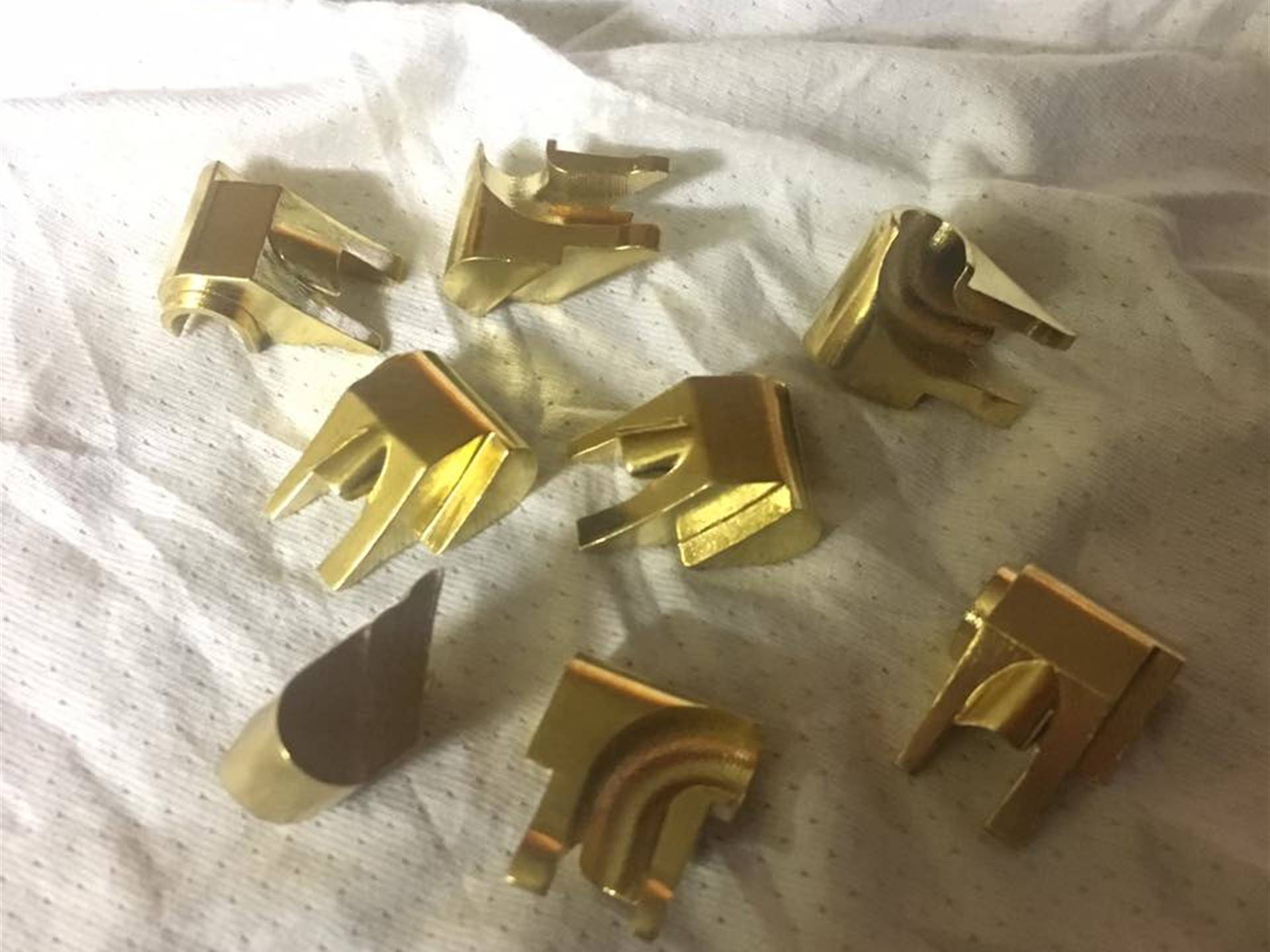
Above is a sample lot of the Bosch Rexroth Ball Bearing Recirculation plugs offered ONLY by Ballscrew Guys. Manufactured from brass, our initial torture tests have shown they can run with greater longevity and reliably than the OEM plastic inserts. These are parts we keep in stock at all times for all the KOMO Rexroth ball screws. So we are ready on short notice to come and repair the X or Y (or V) Axis of your machine, with the least downtime possible. Please note, if you request or your ball screw requires this upgrade, it will be an additional flat charge to our set, upfront pricing.
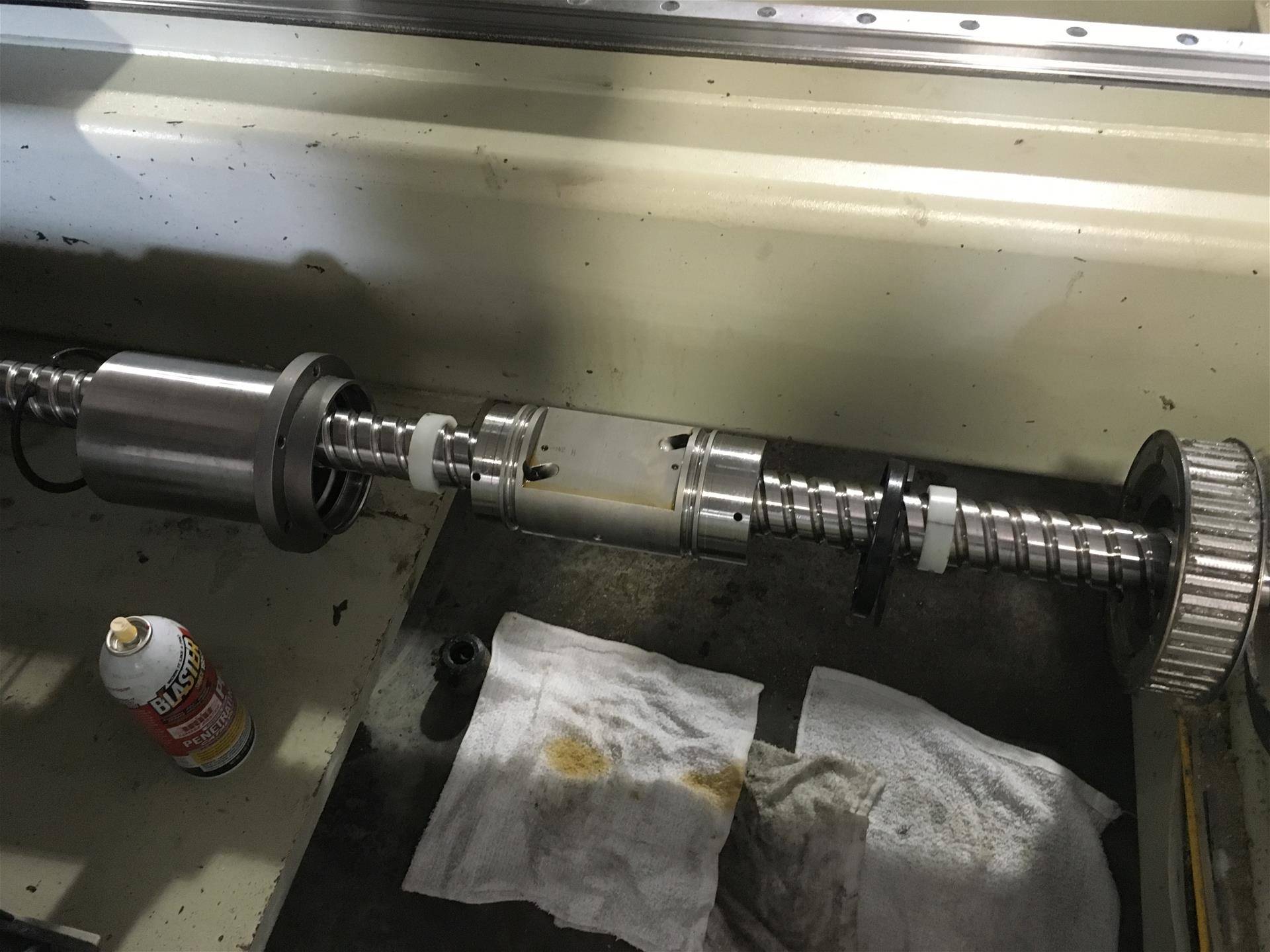
Shown is the NSK External Rotation Bearing from a KOMO X-Axis screw disassembled and spread along the screw for the final cleaning before reassembly. The Rotation Bearing housing is pulled aside. The interior ballnut is completely cleaned and flushed out. If needed, new protective seals are installed, also a product provided by Ballscrew Guys. By rebuilding the ballscrew in the machine, valuable downtime is avoided, getting your machine up and running as soon as possible.
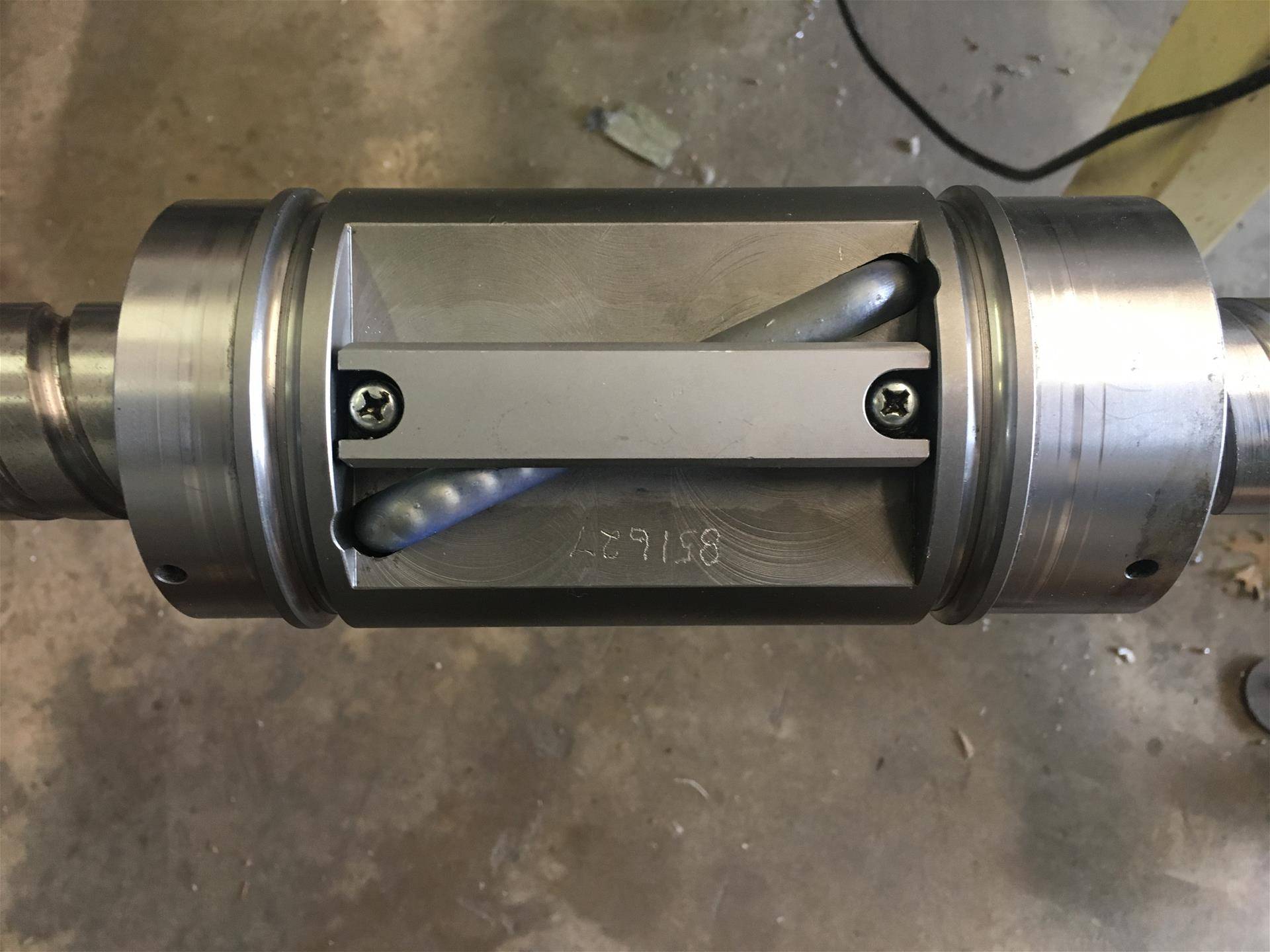
This image is showing one of our design prototypes for manufacturing our own return tubes. Testing and verifying that our part geometry is compatible with existing NSK Ballnuts and ball screw shafts, before we have a production lot manufactured from steel. This tube is made from clear plastic and is quite helpful in demonstrating how certain lubrication types flow along with ball bearings.
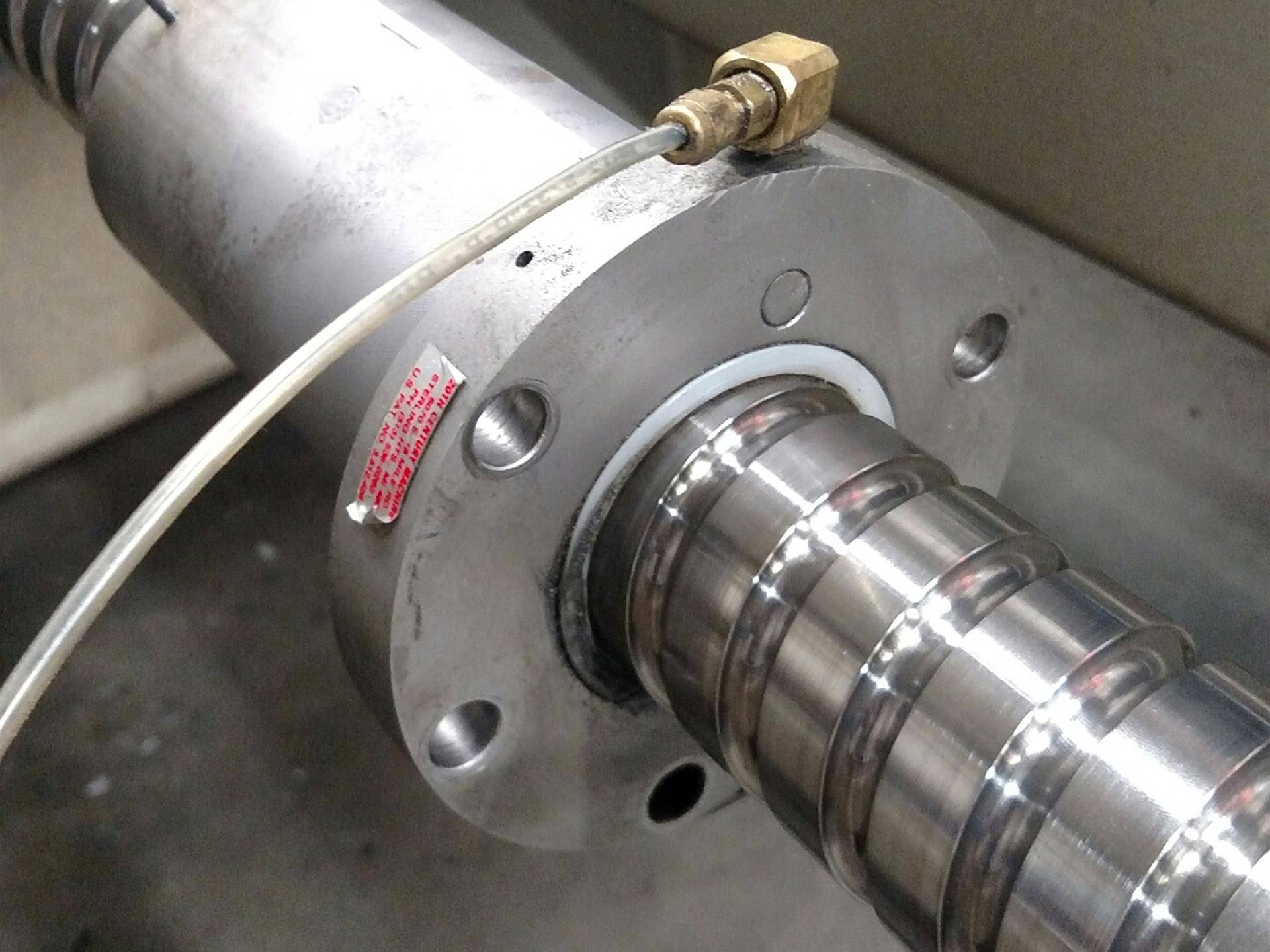
This is a 20th Century Machine (TCM) ball screw found on an older, pre-2000 machine. TCM was bought out by SKF at the end of 2002. Finding parts for these are sometimes problematic. This type of ball screw is a fixed nut type, where the ball shaft is connected to a drive motor that spins it. This type of Ball Screw requires service similar to the Bosch Rexroth types, as the ballnut has to be completely removed from the shaft for refurbishment. Often these types have restrictive collars pressed on the end which act as a spacer to butt up against End Bearings.
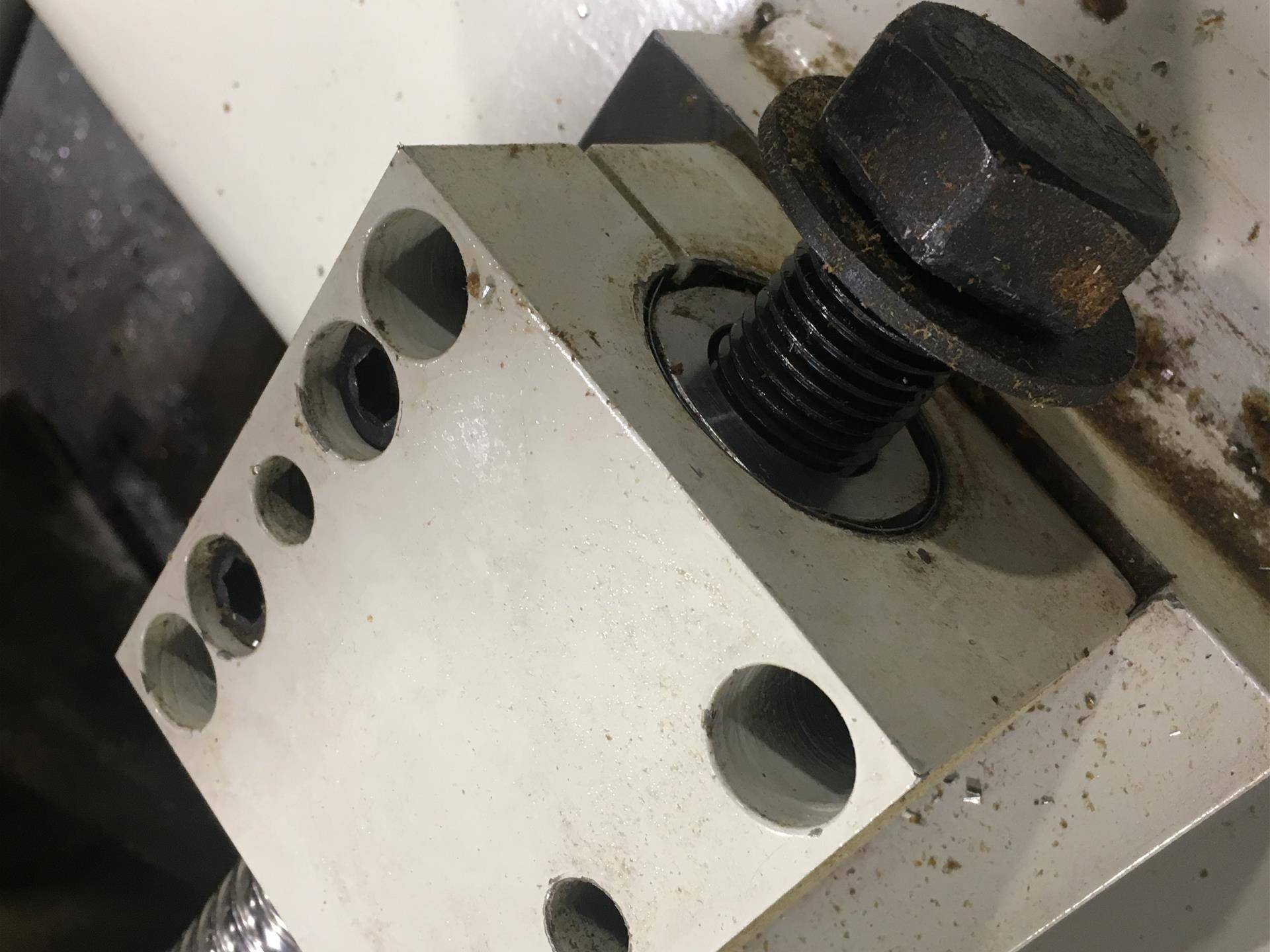
Ball screw tension is important when servicing the motion systems on the KOMO. Both the Bosch Rexroth and NSK External Rotation Bearing types of ball screws rely on moving back and forth on a fixed and stretched screw. Ballscrew Guys typically does not charge for ball screw tensioning service as part of our regular service packages. We feel that it is part of the overall service. Nor do we charge for the removal of the ballscrew end mounts on either side of the machine to service the screw, or replace belts.
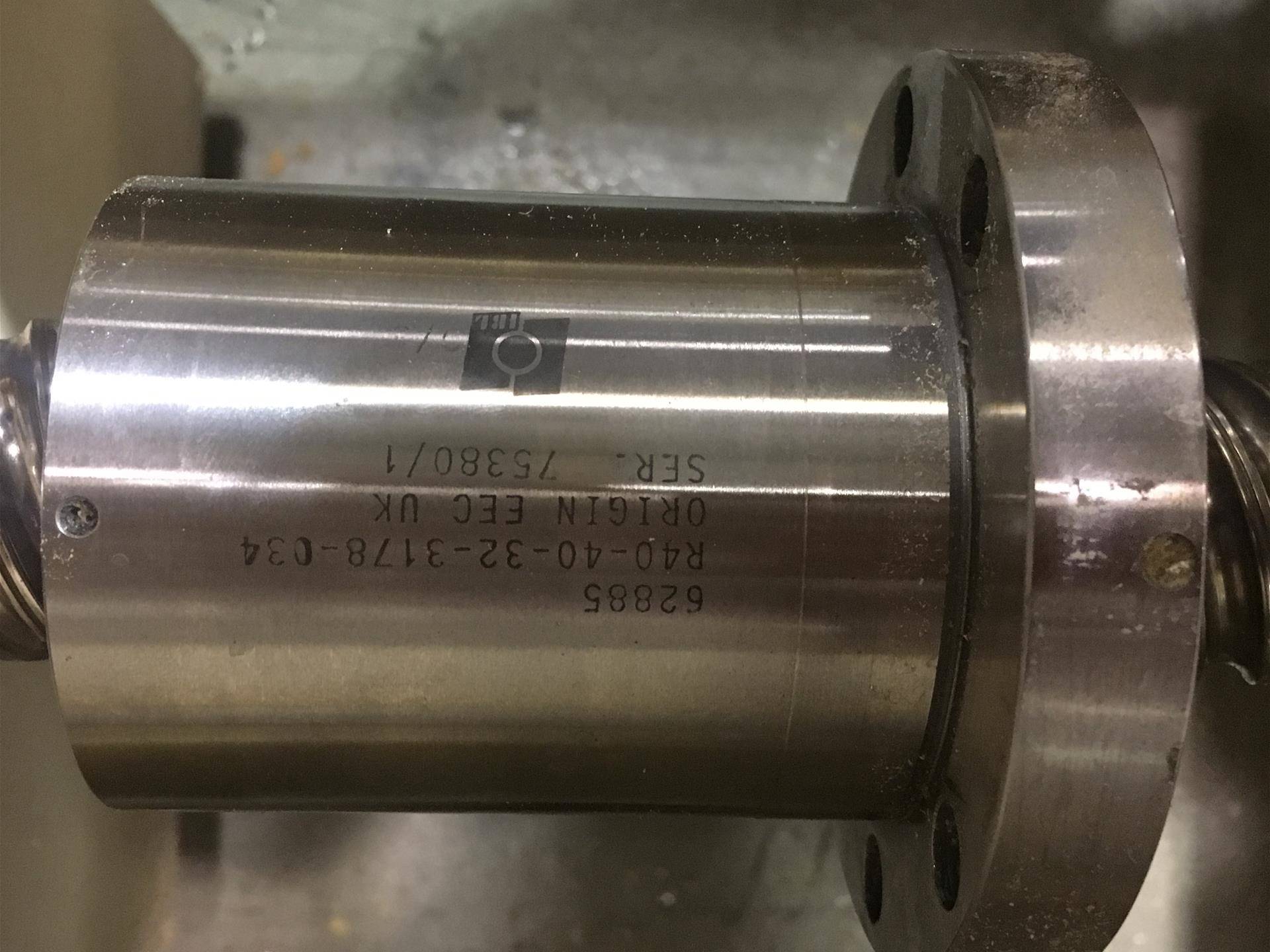
Another ball screw type found in the older, Pre-2000 KOMO milling centers. This is an IBL Screw. If you examine the ball screw shaft windings, you can see where the Star and Rexroth designs origins came from. This is a discontinued screw which was once made in the United Kingdom. Besides its similarity to the the Rexroth series, it is also like the 20th Century Machine (TCM) ball screw assemblies where it has a pressed collar on the the end, locking the ballnut onto the shaft, while acting as an End Bearing spacer.
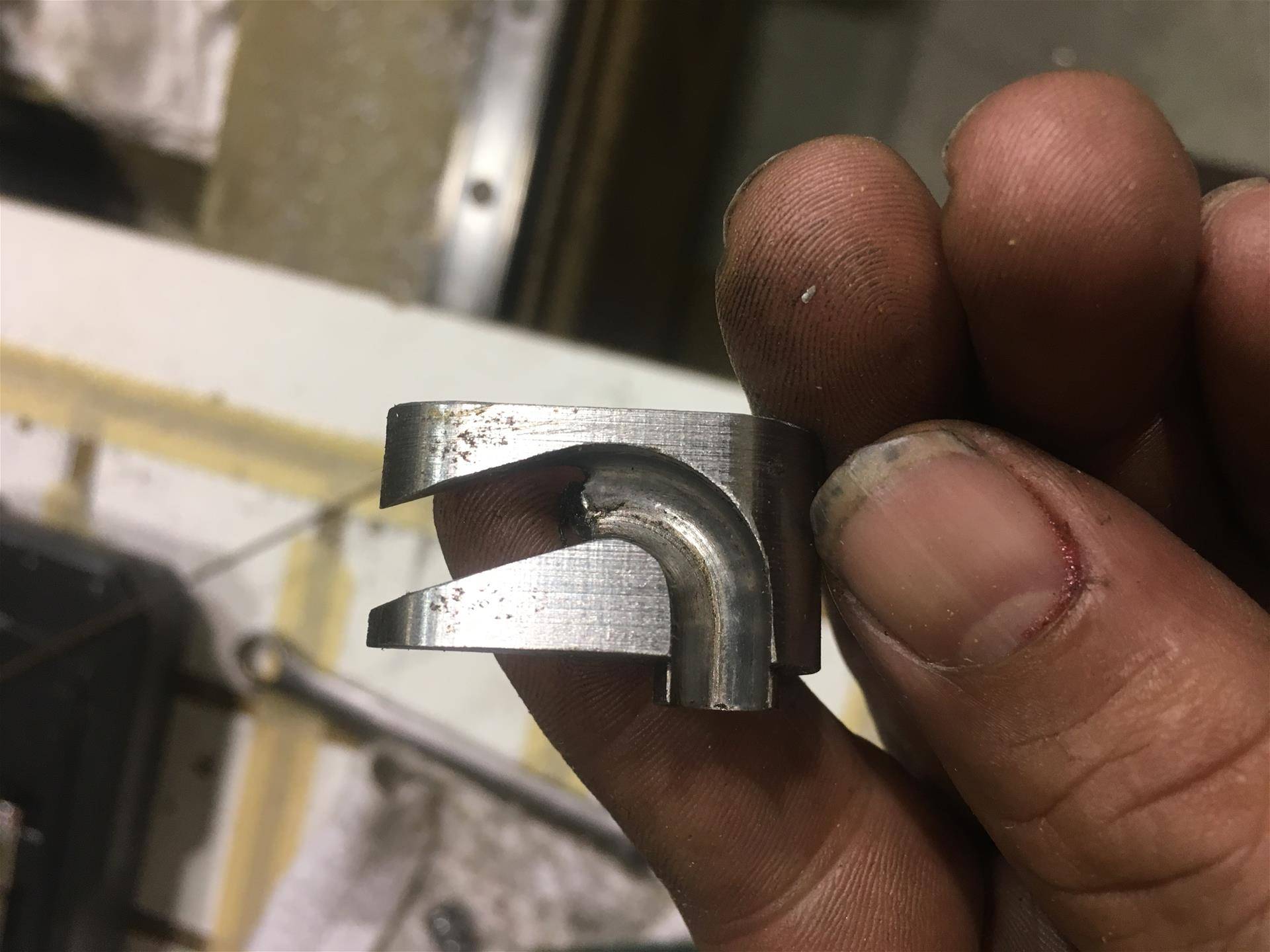
This image shows some of the inspiration behind Ballscrew Guys having our own Bosch Rexroth style ball bearing recirculation plug or shoes designed and fabricated. The UK made IBL screws show the origins behind the Star and Rexroth designs. This part is machined from steel and has been running for well over 20 years. It is found typically on the older KOMO milling machines.
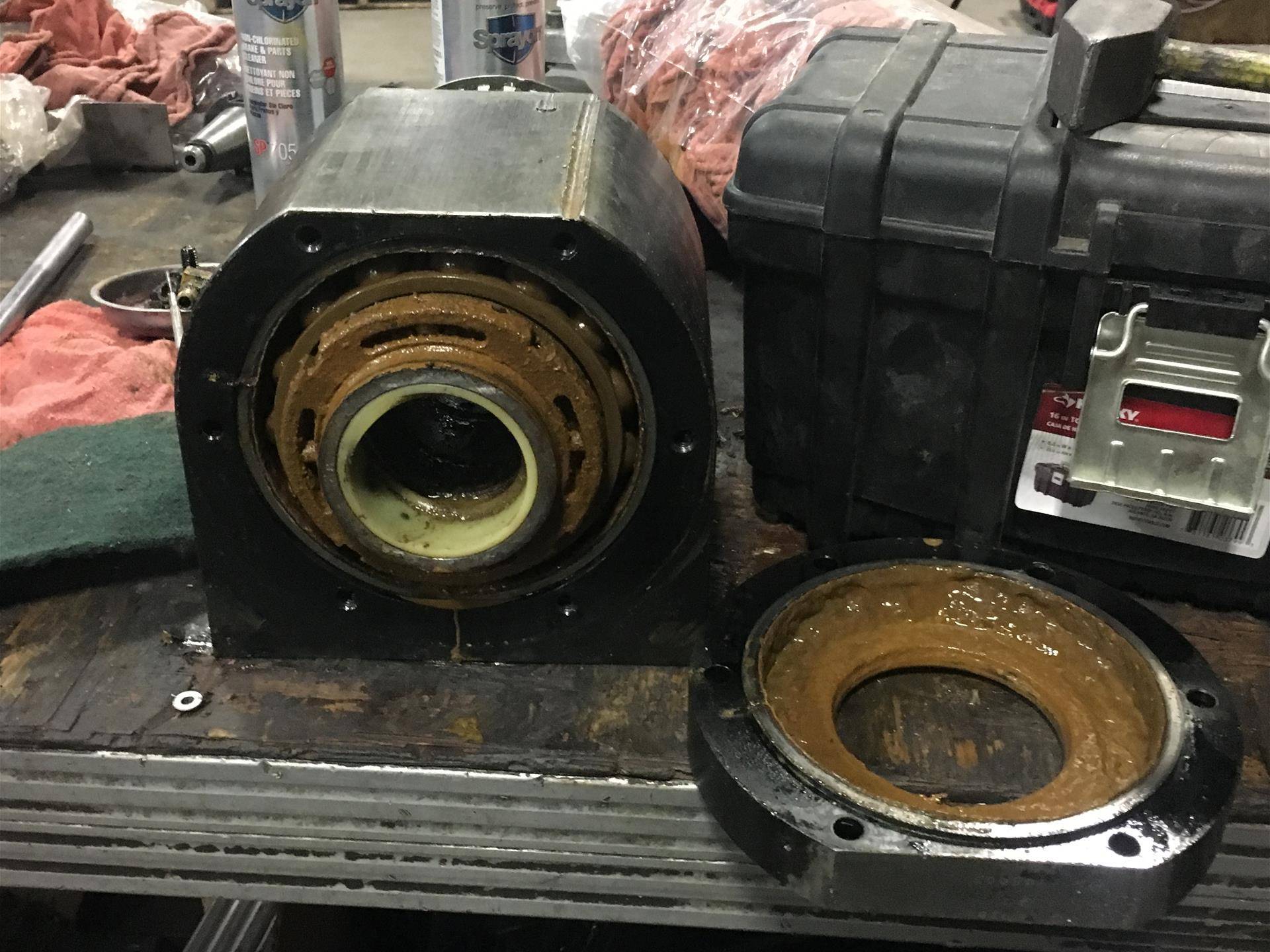
This is the entire Ballnut and Rotation Bearing Assembly from a KOMO VMC 40/180 milling machine used exclusively for aluminum products. The entire assembly has corrosion issues based on a water based cutting fluid and a less than stellar maintenance history. On this model of ball screw assembly, the rotation bearings are NSK End Bearing styled, with massive pumpkin balls inside. When Ballscrew Guys service these types of screws, we have found that the massive bearings are corroded and need of replacement. We strongly suggest ordering them prior to ballscrew service, and Ballscrew Guys can provide you with the size and part number ahead of time. Saving you valuable time, as these bearing parts will take some time to reach you from the other side of the Pacific Rim. We Know. Please understand if you are seeking to have your KOMO VMC and like sized machines serviced, our regular flat rate pricing might not apply. Machines like this, in our decades of experience, are major surgery. Refurbishment can take several days.
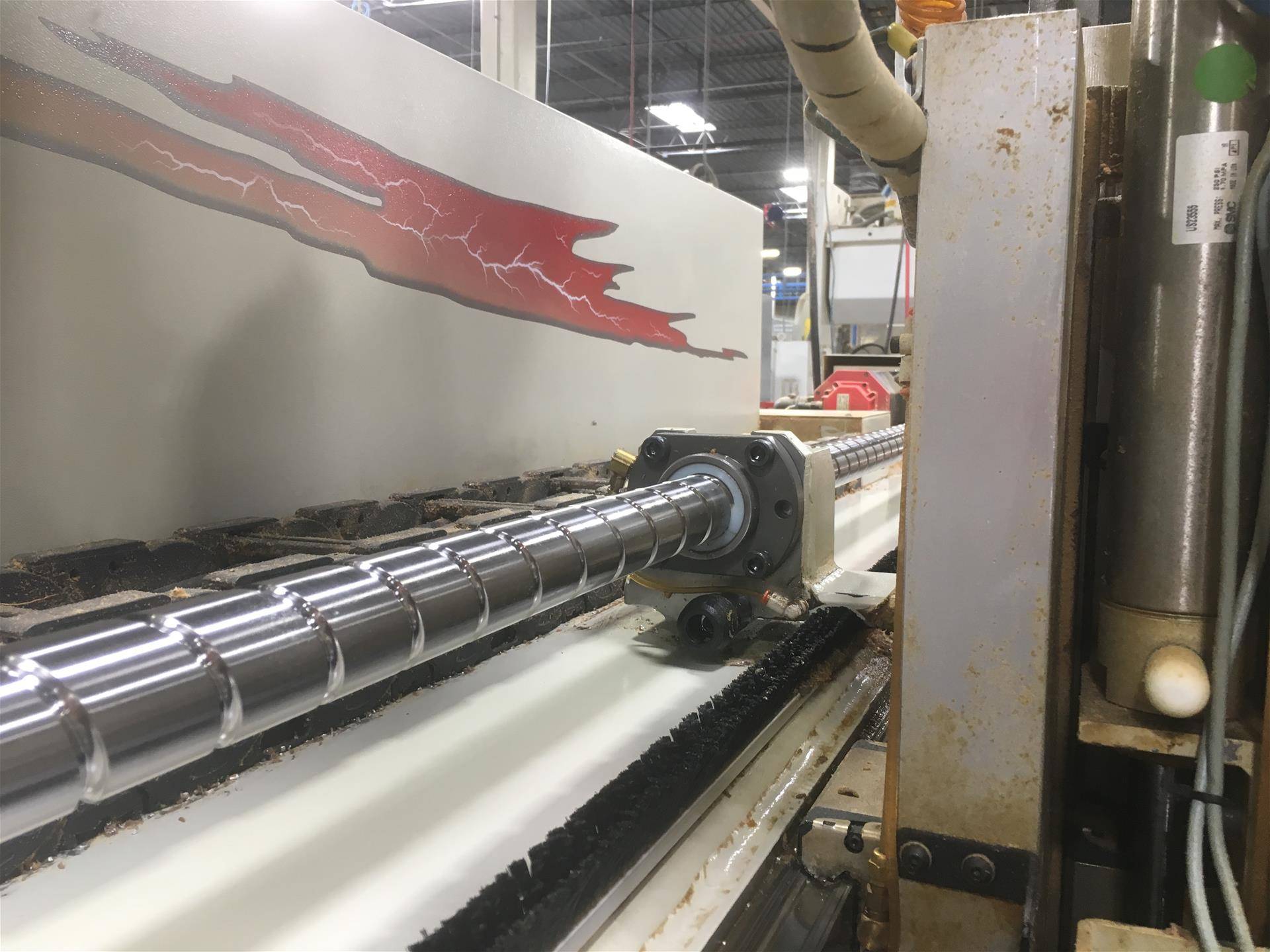
Cleaning out the Y-Axis to service the Ball Screw.
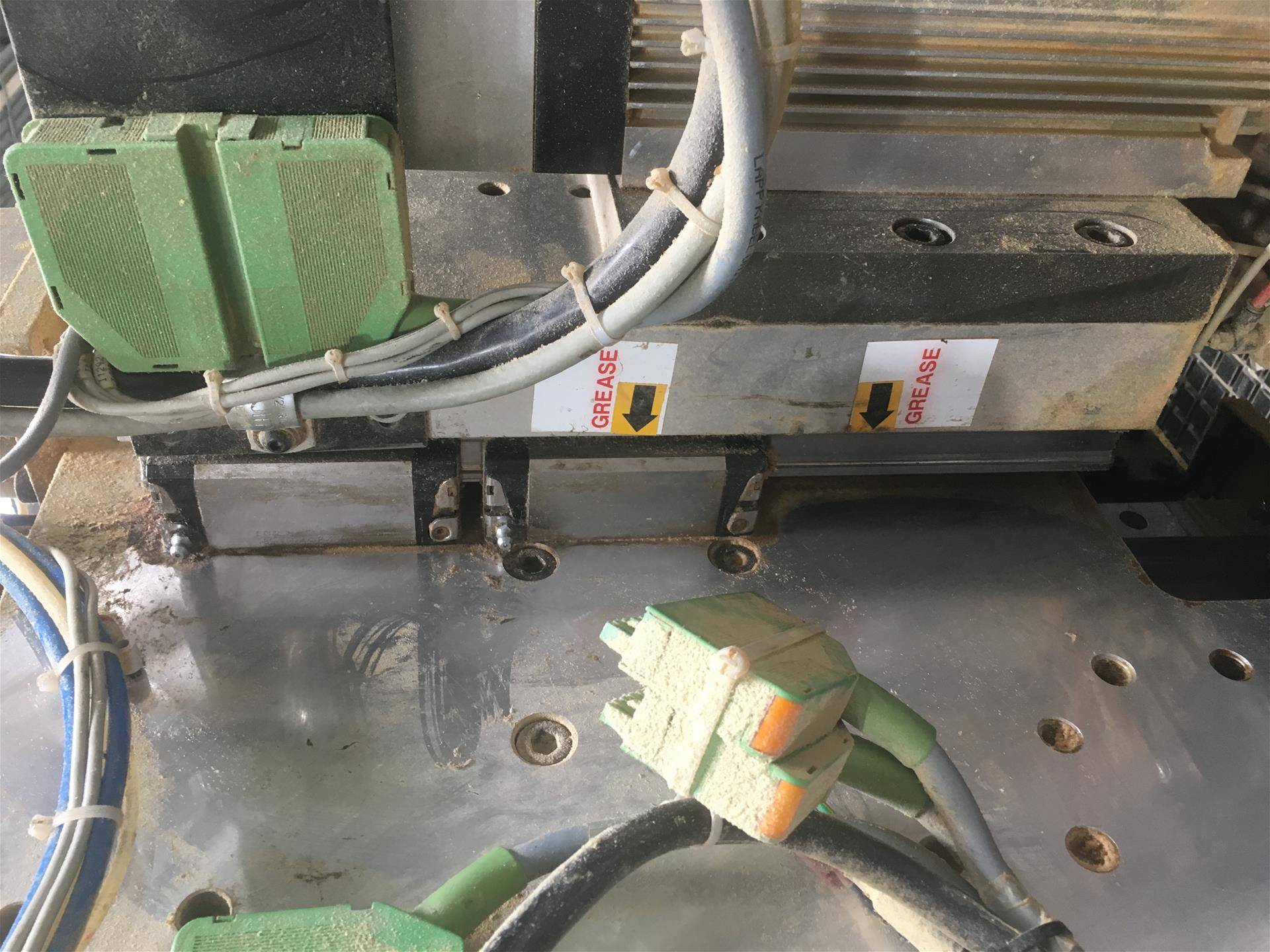
So often overlooked, the Linear Way Guide Blocks on the Z-Axis often are forgotten about. They need regular lubrication, just like all the other bearing based CNC motion systems.